Xbox Controller 1708 - Right Stick module replaced, then up input of either 80%+ or 100%
Those poor pads...

I dove into learning how the potentiometers work to try to understand why these munched connections were leading to a 100% direction.
I knew one or more of the three round pins on the side were my problem, relating to the vertical up/down movement of the stick.
Looking at RDC's PCB scans, traces and info here
https://acidmods.com/forum/index.php/topic,43981.0.htmlTop pin is the ground.
Middle pin is the wiper/arm - it moves as the stick is moved up/down. It gets a reading for the position of the stick and feeds it elsewhere on the board.
Lower pin is the input - where the power is coming from.
When the stick is pulled down the wiper rotates closer to the input. There is less resistance here so the wiper carries a higher voltage.
When the stick is pushed up the wiper rotates further from the input. There is more resistance here to the wiper carries a lower voltage.
So when there is little to no connection to the wiper there is low voltage and it interprets this as the stick being pushed far forward.
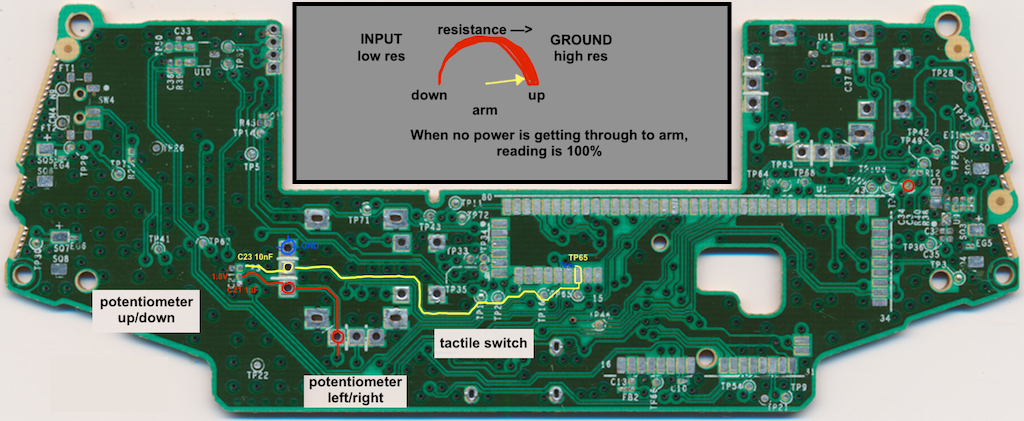
...
I tried several times to smudge the solder against the scraped traces but had no luck.
So again referring to RDC's comments I researched how to use wires to jump to the correct TPs.
I used the wires from the dual vibration motors (I always turn this off anyway, personal preference) and connected:
Top pin to another ground connection that was in decent condition.
Middle pin to TP65 over near the SOC board.
Lower pin to TP103 / the left pin of the three RX potentiometer pins along the bottom.
And she's alive!!!!

If fixing RX the left pin links to TP103, the middle pin to TP66 and the right pin is ground.
These are the grounds
